I noticed that at the holiday time everyone likes to turn "inside out" ornaments.
So I decided to see if you could model it.
Below is my first try. Haven't yet figured out how to turn the outside profile.
Saturday, November 22, 2008
Wednesday, September 24, 2008
Eucalyptus Clock
A clock turned from Fiddleback Eucalyptus.
It was first modeled in SketchUp.
More detail at www.turnedooutright.com
Friday, August 22, 2008
Modeling "Leaf Extraodinaire"
In this months issue of American Woodturner Tim Yodler teaches us how to turn a "German Ring turning".
I couldn't leaf this idea alone, I just had to try and model it. I haven't tried turning it yet but I think that turning is way harder than modeling it.
This model made my PC groan! Below are some hints on the process.
The finished model
Turn it on the Virtual Lathe
- Imported a leaf graphic to use as a model.
- Draw with line tools over it on the grid insuring it was "closed".
- Then "turn it" on the virtual lathe

Getting the 1/8 section
- Group and copy the entire turning to the right of the lathe
- Insert 4 panels into the truning to create the angled surfaces
- Select it all and ungroup every thing
- With it all selected "intersect" it
- Delete all the surfaces except for one 1/8 section
That was fun! Now I need to turn one, not so easy?
Donnie
Sunday, August 10, 2008
Holy Water Font
I just completed the Holy Water Font. Above you can see the model and the finished project.
This project included many disciplines, woodturning, inlays, guilding and metal spinning.
In this post I will focus on the modelling part of the project. Turning details can be found at Turnedoutright.com.
View Extents
Above you can see all the objects of the model. The main part of the models object can be seen on the virtual lathe. These parts were assembled and colored to the right.
Turning at the Virtual Lathe
Turning at the Virtual Lathe

Seen in this close up all the components were modeled in the round. Then the halfmoons (lower right and left of the back) were subtracted from the back by intersecting 3D circles with the model. Note: I decided not to use these in the real model. Also the ring that held the AL dish was designed with a solid bottom but I made it an open ring during turning since I was afraid it would retain water.
The Rings
The rings were also modeled in 3D. I decided to use the flat model on the right for the actual carving but used the 3d version on the left for the model printouts.
The AL Dish
The AL Dish
This story stick printed full scale was used to make the spinning mandrel.
The Final Assembly
The Final Assembly

Above you can see the final assembly, where the fit was tested.
More turning details at www.turnedoutright.com
Go buy the book "Woodturning with SketchUp"
Sunday, August 3, 2008
Here is a challenge for you!

I did this staved vessel model using SketchUp.
Let me know if you figure out how to do it or one beter. I'll post your accomplishment.
Labels:
SketchUp,
staves,
vessels,
Woodturning with Sketchup
Saturday, July 5, 2008
SketchUp Plugins
I like to watch the blogs looking for new SketchUp plugins.
I've created a window Box.net folder so that you can easily get to them.
Note that in the MENU of the window you can subscribe to a feed that will notify you when new plug-ins are available.
Enjoy!
I've created a window Box.net folder so that you can easily get to them.
Note that in the MENU of the window you can subscribe to a feed that will notify you when new plug-ins are available.
Enjoy!
Friday, June 27, 2008
SketchUp for Dummies

A couple of users have asked about a starting book on SketchUp to use prior to "Woodturning with SketchUp".
Here is a link to "SketchUp for Dummies".
It is available at most book stores.
Saturday, June 21, 2008
Saturday, May 3, 2008
Mothers Day Music Box


The music box is complete.
This project could not successfully have been completed without modeling. Just one more example of how SketchUp and "Woodturning with SketchUp" can broaden your capabilities.
Note the video on the side bar and on the turnedoutright woodturning channel.
More posts in this blog on the Music Box:
Monday, April 14, 2008
SketchUp Recognizes Woodturning
This week we got an awesome mention in the SketchUp blog.
This is great exposure toward the advancement of "3D Woodturning Modeling".
"I was just alerted to the presence of a really neat blog about using SketchUp for woodturning. It's called Turnedoutright, and it's worth a look -- even if you're not a woodturner yourself. The SketchUp models are outstanding."
Thanks to Aidan Chopra
The Music box is completed, watch for final post on the project.
You can get a copy of the "Woodturning with SketchUp" @ the turnedoutright store.
This is great exposure toward the advancement of "3D Woodturning Modeling".
"I was just alerted to the presence of a really neat blog about using SketchUp for woodturning. It's called Turnedoutright, and it's worth a look -- even if you're not a woodturner yourself. The SketchUp models are outstanding."
Thanks to Aidan Chopra
The Music box is completed, watch for final post on the project.
You can get a copy of the "Woodturning with SketchUp" @ the turnedoutright store.
Labels:
google,
sketchup blog,
Woodturning with Sketchup,
woodturnings
Monday, March 17, 2008
Music Box Lid: Chip carving
The music box project is progressing along as planned.
I got to the point where the lid was turned.
I was pleased with the lid but realized that some surface treatment would add a nice touch.
So I went back to SketchUp and modeled a pattern to carve on the lid.
IT WAS EASY TO DO:
- Draw out a circle the size of the lid, this also provides a drawing plane
- Add an internal circle that matches the center (not to be carved) of the lid.
- Divide the circle up with the protractor into four quadrants
- Use SketchUp drawing tools to make a pattern in one quadrant
- Then copy and flip it into the other quadrants.
- Print full size
- Lay over lid and trace the pattern with graphite paper
- Carve away!
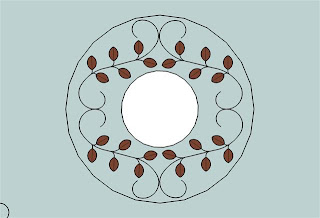
Soon I will post the completed project on turnedoutright.
Donnie
Labels:
music box,
SketchUp,
Woodturning with Sketchup,
woodturnings
Saturday, March 8, 2008
Tip: 3D story sticks
Last night while I was finalizing the music box plans I discovered an easy way to make a story stick on the virtual lathe that is actually a full size 3D cross section.
The following instructions assumes that you have read the book "Woodturning with SketchUp" available on turnedoutright.
To review, one of the useful things to do after you competed your computer design is to print a full scale drawing of the turning. This story stick allows you can take measurements directly with your caliper. I don't like to have to do math when I'm standing in front of the lathe, no not even multiplying by 2x :)
Normally I print a cross section view (requires that I multiply measurements by 2x) or a 3D view (doesn't show internal dimensions) and go to the shop.
Better approach:
The following instructions assumes that you have read the book "Woodturning with SketchUp" available on turnedoutright.
To review, one of the useful things to do after you competed your computer design is to print a full scale drawing of the turning. This story stick allows you can take measurements directly with your caliper. I don't like to have to do math when I'm standing in front of the lathe, no not even multiplying by 2x :)
Normally I print a cross section view (requires that I multiply measurements by 2x) or a 3D view (doesn't show internal dimensions) and go to the shop.
Better approach:
- After drawing the cross section make a copy to the right of your original and render it in 3D, all on the "grid background".
- Then click on the cross section tool [Menu: tools/section plane] and drag it to the "Grid Background" plane and click on an intersection of the grid lines. This will put the crossection on the same plane as the grid and therefore it will show up on your story stick.
- SketchUp will slice the rendered pieces at the centerline of the lathe showing internal and external dimensions in full scale.
- Print full scale and take to the shop.
- Now all your measurements can be taken directly by setting your caliper to match the drawing.
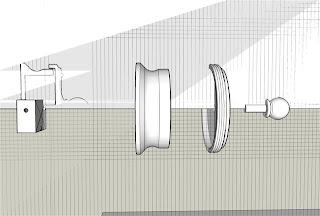

New Sketchup Video Links
I have added a couple of really good SketchUp video links under Useful links in the sidebar .
This is a great place to learn, refresh and update your SketchUp Skills.
Here is the link to the new turnedoutright UTube Channel
Enjoy!
This is a great place to learn, refresh and update your SketchUp Skills.
Here is the link to the new turnedoutright UTube Channel
Enjoy!
Monday, February 18, 2008
"The Mothers Day Music Box Model"

I decided to take on another modeling and turning challenge.
Inspired by the book "Masterful Woodturning" (ISBN 0-8069-8709-X). I decided to combine woodturning and music boxes.
Design goals for the Music Box project:
- Box with a removable lid
- Made from a burl
- Music box hidden inside
- Animation
- Wind the music box without opening top
- Pleasing shape
This meant that the box would be multiple pieces that would need to fit together with relatively tight tolerances.
Here is how the entire project was then modeled on the Virtual Lathe in 1-1 scale.

Step1:
The music box itself was modeled. It became obvious that the center of rotation of the music box was offset. This meant that the bottom would have to be quite a bit larger than the music box.

Step 2:
Just as if you had sliced the final assembly down the middle, draw the 1/2 cross section of the entire assembly on the grid making sure to interpose all the components like they will fit in the final assembly. In this design there is a music box, base, top, finial and coupler. Notice how the model of the music box is used to get the dimensions correct in 2 and 3D.
HINT:I like to create the cross section first then perform a few trial and error renderings by rendering it then "undoing". After I get the design the way I like it I make a copy of the cross section to the right on the grid. Always keep at least one copy of your 2D cross section "un-rendered" so that you can come back later and make modifications. You will also need the 2D version of the model to make a story stick.
Step 3:
This project has multiple components so make a copy of the 2D cross section to the right and then separate the components horizontally into individual pieces. Render them as four 3D components.
HINT: An easy way to do this is to select the line segments that belong to each individual component and group them. Then move all that components line segments as a group. Once the components are separated on the grid render and group them as individual 3D items. Then group all the 3D groups before you copy the entire assembly to the right off the lathe.

Step 4:
Move and copy the entire assembly to the right and then rotate it vertically. Note the music box offset in the bottom so the shaft is on the center line of the top.

Step 5:
Make yet another copy of the entire assembly. Explode it into separate grouped components. Then assemble the music box using these components to give a final view.

Step 6:
Using the section tool create a sectional view through the entire piece to check for internal interferences. As you can see the coupler has a problem it seems to long!
Step 7:
Using the dimensions from the 2D cross section as my guide, I found some redwood burl the right size. I guess its time to go to the shop!
Enjoy!
Donnie
Go to the Turnedoutright WebShop!
Go and get the "Woodturning with SketchUp" book
Labels:
free software,
Modelling,
SketchUp,
turnedoutright,
woodturnings
Tutorial on "Woodturning with Sketchup
I have been working on ways to better introduce my book "Woodturning with SketchUp".
Click on the UTube video in the side bar to review the tutorial or click here: Tutorial on "Woodturning with SketchUp".
Click on the UTube video in the side bar to review the tutorial or click here: Tutorial on "Woodturning with SketchUp".
Subscribe to:
Posts (Atom)